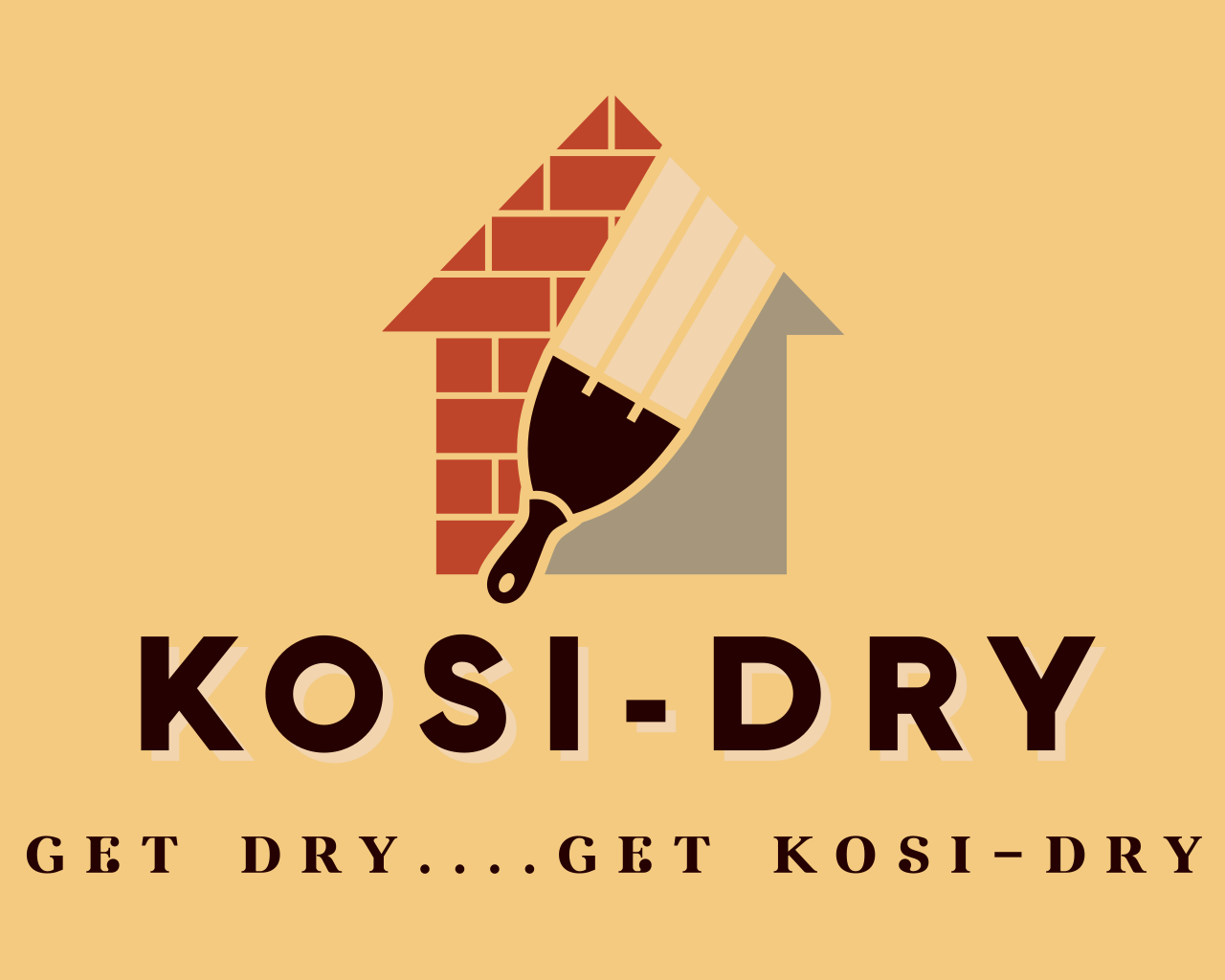
Is your home:
Cold?
Damp?
Wet?
Under insulated?
Spending a fortune on heating bills?
Old building or new building.... it doesn't matter!
Our product will perform as advertised and you'll never know it's been applied.
This is our work, and we carry it out to the highest standard, giving you the best possible solution to your home issue.
Here at KOSI-DRY we strive to make your home warmer, more cost affective and isulation efficient while protecting against the British elements.
So please read away and get informed on the latest of technology-led aggregate protection, so you can make the best decision to GET DRY.... GET KOSI-DRY.
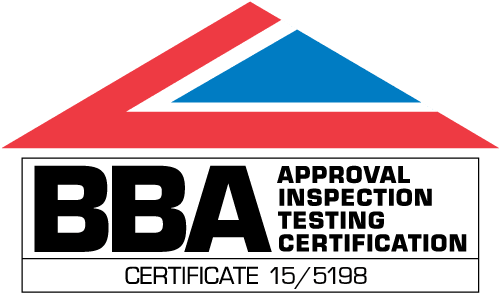
Masonry Protection Cream
- Fast acting!
- Enhancing water resistance for 25 years
- Effectiveness on concrete, mortar, brick, and sandstone.
- Strong and resistant aggregate technology
- BBA approved
- Inconspicuous application
- UK's leading aggregate protection product
- Supporter of sustainable and economic solution's
What is Penetrating Damp?
Rain penetration through masonry (known as penetrating damp) is a common problem in buildings – particularly in the case of those of solid wall construction. The problem is also increasingly common in buildings of cavity wall construction where cavity wall insulation has been poorly installed or used in walls that are not suitable for cavity wall insulation. Other paths through which rain can cross through a cavity wall include incorrectly positioned wall ties and mortar obstructions in the cavity.
Symptoms of Penetrating Damp
Older buildings, especially with solid walls, are more likely to suffer from penetrating damp. We are aware that the symptoms can often take weeks or months to appear. The symptoms we look out for when identifying penetrating damp are:
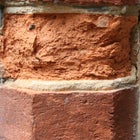
Brick damage — Moisture entering the brick (known as spalling) causes surface damage
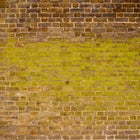
Moss — Excessive moss growth on external walls.
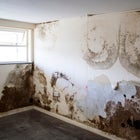
Mould — Mouldy smell or signs of mould growth on internal decoration
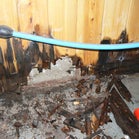
Wet Rot — Rotting skirting boards or timber.
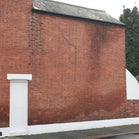
Localised dampness — Blotchy patches on internal walls.
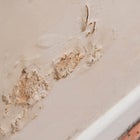
Plaster damage — Plaster & paint deterioration, blistering, appearance of stains & salts.
Causes of Penetrating Damp
Penetrating damp is caused by water permeating through walls from the outside. It can occur at all levels of a building but is more prevalent higher up. It is possible for damp to move within walls but this horizontal movement differs from the vertical movement of rising damp. Penetrating damp is usually caused by the following:
Porous Walls — Aging bricks lose the ability to keep out rain penetration.
Spalled Bricks & Degraded Mortar — Damage to brickwork allows water to penetrate.
Building Defects — Defective guttering and downpipes, roof damage, dilapidated or poorly installed windows. In this case fix the root of the problem before applying KOSI-DRY to boost your protection.
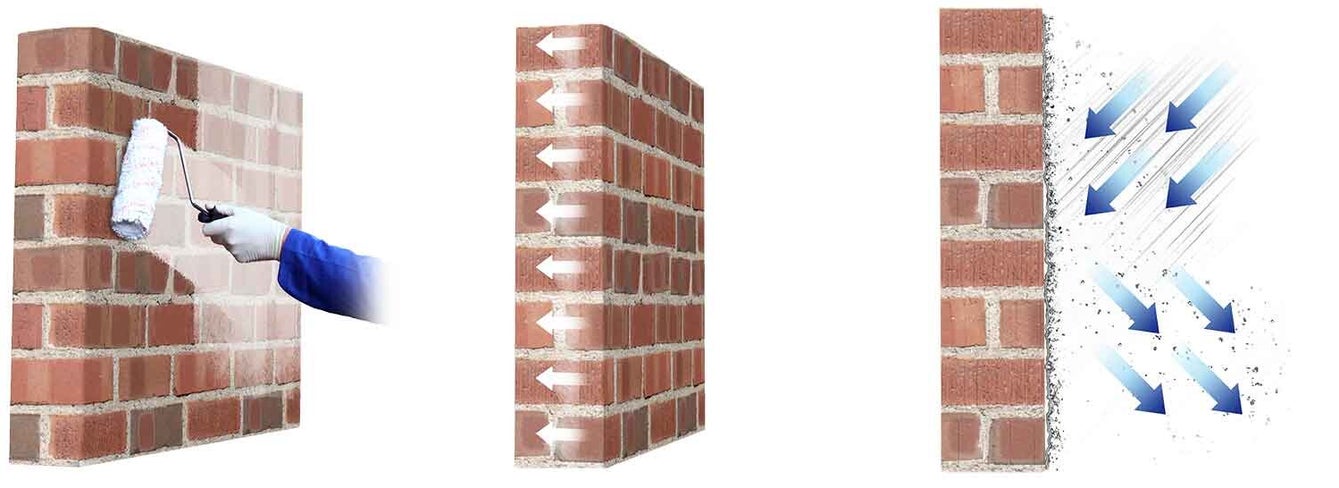
Maintain the Natural Appearance of Your Walls
Breathable, Colourless Protection from KOSI-DRY masonry protection cream, applied to masonry in a single coat by means of brush, roller, or spray. Once applied, it penetrates deep into the masonry before curing to form a colourless, breathable water repellent barrier.
What is KOSI-DRY Masonry Protection Cream?
KOSI-DRY is a deeply penetrating water repellent cream for brick, stone, and concrete. Due to its cream-based formulation it is able to penetrate more deeply into masonry than standard liquid-applied water seal products.
KOSI-DRY is based on proven silane/siloxane technology and works by lining the pores of the masonry rather than blocking them - allowing the wall to continue to breathe. This is in contrast to many standard brick sealer and stone sealer products which coat the masonry with a thin film.
KOSI-DRY is easy to apply using a brush or roller and only a single coat application is required - many competing water repellent products require two coats.
25-Year Durability of KOSI-DRY is our guarantee, the only colourless masonry water repellent treatment that carries BBA approval (cert. number 15/5198). After extensive testing to determine continued water-repellency after aggressive freeze-thaw and UV exposure, the BBA issued a certificate with the following durability statement:
"The product will remain effective as a masonry water repellent for 25 years".
"Dry walls are warm walls".
KOSI-DRY ensures that the masonry remains dry throughout the year – maximising its thermal resistance or "R" value. Dry walls are better insulators than wet walls.
Flood Protection
When we use KOSI-DRY in conjunction with KOSI-DRY Repointing Additive No.2, KOSI-DRY is able to increase the flood resistance of masonry without altering its appearance.
KOSI-DRY Preparation & Application
KOSI-DRY is only applied to dry, porous surfaces. It's main purpose is intended for above ground use only. We only apply our product when rain is not forecast for the next 24 hours. Hairline cracks up to 0.3mm can be ‘bridged’ by KOSI-DRY however, it may be necessary for us to fill cracks in brick/ stonework and repoint using a suitable sand/lime or sand/cement mortar incorporating KOSI-DRY Repointing Additive.
Dirty surfaces will be cleaned before the application of KOSI-DRY Masonry Protection Cream to the recommendations given in BS8221-1:2000, “Code of practice for cleaning and surface repair of buildings. Cleaning of natural stones, brick, terracotta and concrete.” Application to structures containing high levels of salt is still under interpretation for feedback.
Test Area
KOSI-DRY has been formulated to be colourless once cured. However, very slight darkening may occur when it is applied to some substrates. Although this will usually fade over time, a small, representative and inconspicuous test area should always be treated before full treatment begins.
Application Process
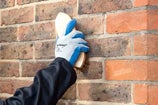
Application around details such as windows, ledges and brick joints.
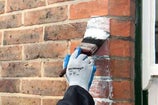
We use a brush to apply around intricate details such as as windows and harder to apply areas.
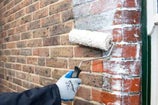
15-20 minutes after application, the formula starts to penetrate into the masonry.
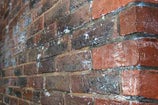
After 24-48 hours the wall will have returned to its original appearance.
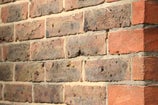
The masonry will be resistant to light rain after two hours.
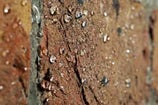
The surface area after KOSI-DRY'S many years of protection.
25-Year Durability BBA approval
Being approved by the British Board of Agrément (BBA) Certificate Number 15/5198.
KOSI-DRY the only colourless masonry water repellent treatment that carries BBA approval. After extensive testing to determine continued water-repellency after aggressive freeze-thaw and UV exposure, the BBA issued a certificate with the following durability statement:
"The product will remain effective as a masonry water repellent for 25 years".
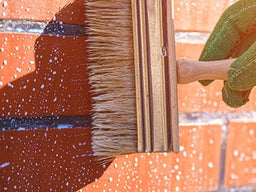
BBA Certification: Certificate Number 15/5198
KOSI-DRY was granted BBA Certification in March 2015 with a stated durability of 25 years. A number of laboratory tests were carried out by the British Board of Agrément (BBA) as part of the certification process.
Test Aims
To provide our customers with ease of mind through independent verification of product performance and to allow KOSI-DRY to be used in conjunction with insulation measures carried out under ECO and the Green Deal which require 25-year durability.
Summary of Tests Carried Out
Water Vapour transmission tests were carried out in accordance with BS EN 12572 : 2001 Hydrothermal Performance of Building Materials and Products – Determination of water vapour transmission properties in order to test the “breathability” of samples treated with KOSI-DRY compared with that of untreated samples.
Water Absorption
Tests were carried out in accordance with BS EN ISO 15148 : 2002 Hygrothermal performance of materials and products - Determination of water absorption coefficient by partial immersion in order to test the effectiveness of KOSI-DRY reducing water absorption compared with untreated samples.
Accelerated Ageing
The water absorption tests (see above) were carried out before and after aggressive accelerated ageing using UV and freeze-thaw.
Test backed Guarantee
UV aged - In accordance with BS EN ISO 4892-3 : 2000 Plastics – Methods of exposure to laboratory light sources – Part 3 Fluorescent lamps. Exposed to UVB 313 lamps cycling 4 hours UV at 50°C followed by 4 hours condensation at 50°C. The samples were removed for testing after intervals of 2000 hours and 2500 hours.
Freeze thaw - Stored in a sealed cabinet controlled at -5°C for 8 hours and then at 23°C and 50% RH for 16 hours. Samples were exposed removed for testing after intervals of 30, 60 and 75 cycles. The depth of Penetration depends on the various substrates prepared for the capillary absorption tests, majority of tests were conducted on natural stone, brick, mortar and sandstone and limstone mixed aggregate's. The samples were broken in half and wetted with water to highlight the depth of penetration of the KOSI-DRY. This was measured at five points across the width of the sample to the nearest half mm. The mean value and the maximum and minimum values were determined and recorded.
Determination of Drying Time
The brick samples prepared for the capillary absorption test were used on completion of the testing. The samples were immersed in water until saturated and then sealed in a vapour impermeable membrane with silicone sealant leaving only the KOSI-DRY coated face exposed. The samples were kept in an atmosphere of 50% relative humidity and at a temperature of 23°C and were weighed at intervals until constant weight was acheived.
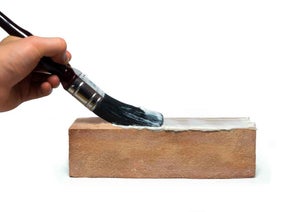
Dry walls are warm walls
We will keep your walls warm with KOSI-DRY by creating a deep water-repellent zone on the masonry surface, KOSI-DRY ensures that the masonry remains dry throughout the year. This maximises its thermal resistance, as dry walls are better insulators than wet walls.
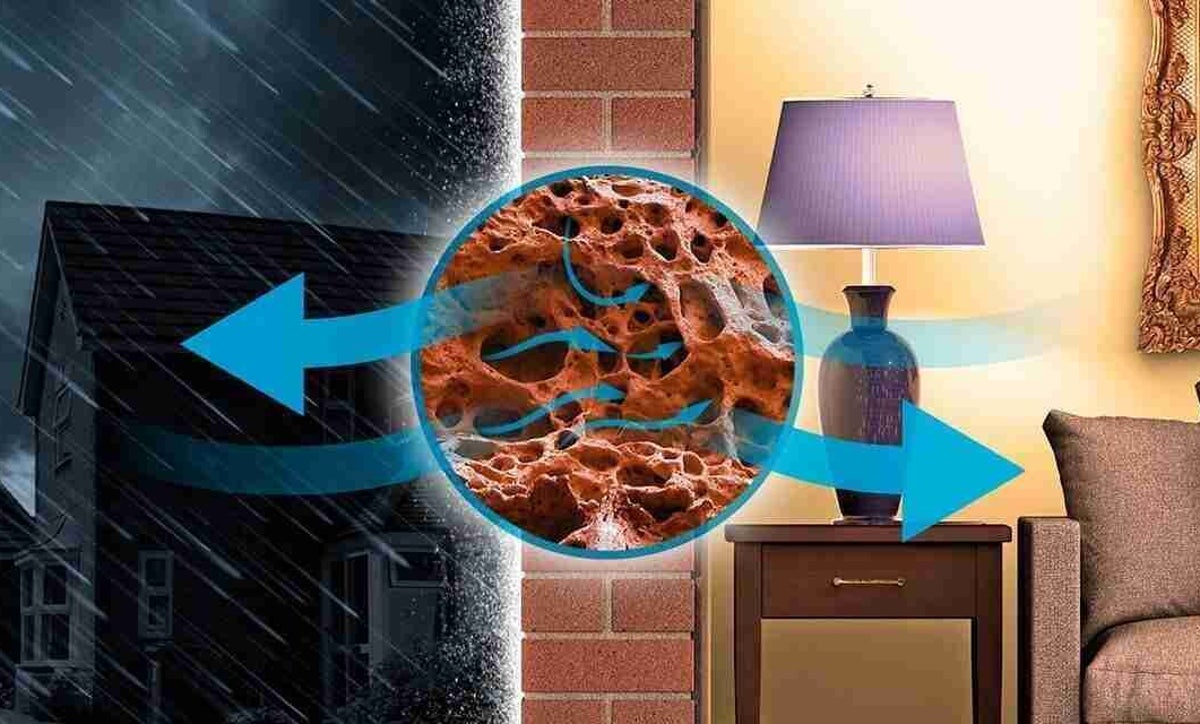
When masonry gets wet it loses its insulation properties, much in the same way that wet clothes make you feel cold. By creating a deep water-repellent zone on the masonry surface, KOSI-DRY ensures that the masonry remains dry throughout the year – maximising its thermal resistance or “R” value.
Reducing Carbon Emissions from “Hard to Treat” Properties
The UK Government has set a target of an 80% reduction in carbon emissions by 2050. Much of this will have to be met by reducing the carbon footprint of the UK’s housing stock.
It is estimated that 85% of UK’s existing housing stock will still be in use in the year 2050 so, even if we build a new generation of “green” homes, measures will still have to be taken to reduce the carbon footprint of the existing housing stock.
"Home but not home free"
Flood resistance system
In most cases, the easiest improvement can be achieved by upgrading loft insulation to reduce heat loss. However, this measure will not address the large proportion of heat loss that occurs through the walls of a building. Where a house is built of cavity wall construction, cavity wall insulation can provide an effective solution. However many houses are built of solid wall construction or have cavity walls that are not suitable for cavity wall insulation (e.g. cavity too narrow). These properties often fall under the “Hard to Treat” or “HTT” category used by housing professionals to denote properties for which reducing energy consumption presents difficulties for technical, economic, or social reasons.
Traditional Insulation Options for Solid Wall Properties
Internal insulation takes up floor space traditionally, but there has been two wall insulation options for properties constructed from solid walls (or from cavity walls that are not suitable for cavity wall insulation). These are internal insulation and external insulation. Both of these types of insulation can be very effective, however, they are not suitable for all properties.
In many cases internal insulation is not suitable because it would cause an unacceptable reduction in room size or is not practical to install without significant disruption to the occupants. External insulation has the effect of altering the appearance of a building which is not always desirable – particularly in the case of buildings faced with brick or stone.
KOSI-DRY offers a Solution
In most cases the thermal resistance achieved by treating masonry with KOSI-DRY will not be as high as those achieved using internal or external insulation. However the use of KOSI-DRY has the advantage of allowing the thermal resistance of walls to be improved on “hard to treat” properties that would not otherwise be insulated. For this reason KOSI-DRY has an important role to play in reducing carbon emissions from buildings. Because KOSI-DRY is applied to the outside of the building, disruption to the occupants is minimised.
Test Work
In order to prove the concept of improving the thermal resistance of walls using KOSI-DRY preliminary test was carried out at the University of Portsmouth comparing the thermal resistance (R-value) of a wet brick with that of a KOSIDRY-treated brick. This test demonstrated that the thermal resistance of the KOSIDRY-treated brick was more than twice that of the wet brick. In order to estimate the thermal benefits of treating walls with KOSI-DRY the real world further testing and modelling was carried out.
Model House Experiment
Further testing carried out by the University of Portsmouth involved the comparative testing of a treated and untreated model house placed in an environmental chamber. During the experiment, the energy required to maintain a stable 20ºC temperature within the model test house was measured. Energy savings of between 5 and 9% were demonstrated in a single brick width wall from the result of changing outside temperature and humidity alone, indicating that energy savings are possible even during periods of no rainfall. A 50% energy saving was demonstrated during a single wet “rain” event.
SAP Analysis and Supporting Data
In order to try and estimate the energy savings possible in the real world data was obtained from BRE and Fraunhofer publications giving examples of moisture contents of exposed masonry walls. This data together with the data obtained from the University of Portsmouth experiments (above) was used to carry out SAP1 analysis on a semi-detatched solid wall house. Depending on the weather locations used reduced heat loss of up to 3 predicted by the model. The SAP model does not take into account evaporative cooling effects which make a small further contribution to potential energy savings.
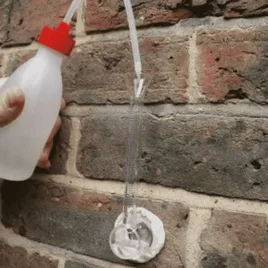
Supercharge Your Flood Protection
KOSI-DRY forms part of a flood protection system, KOSI-DRY can be used to increase the flood resistance of masonry as part of a flood resilience system. When used in conjunction with a cavity drain flood protection system (e.g. Oldroyd), the use oof KOSI-DRY will reduce the amount of flood water that is able to pass through the masonry reducing the risk of floodwater overwhelming the pumping system.
Providing Flood Resilience and Resistance as Part of a Flood Protection System
The problem with lack of defence against flood damage is becoming an increasing reality for many property owners in the UK. According to an Environment Agency report, more than 5.2 million properties are at risk of flooding in England alone (Flooding in England: A National Assesment of Flood Risk, Page 6). Flood damage repairs to unprepared homes can be costly, time consuming and extremely stressful.
An Ideal Solution for Flooding
When thinking about how best to protect your property from flood water, KOSI-DRY products show themselves to be ideal components of both flood resistance and flood resilience protection systems.
KOSI-DRY as Part of a Flood Resistance System...
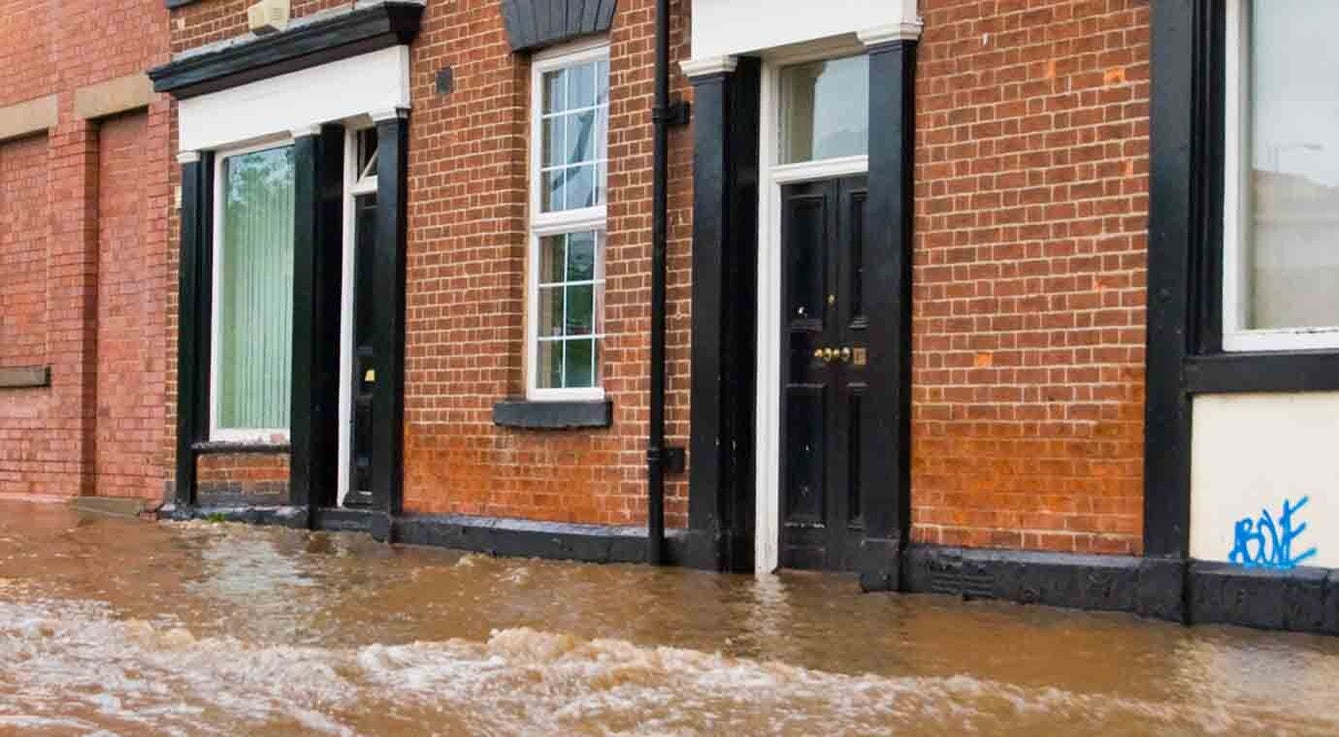
The goal of a flood resistance system is to stop water from entering the property, thereby protecting the interior from damage. This kind of system is best used where repeated renovation or cleansing of the interior after multiple floods is not practical or desired.
KOSI-DRY masonry Protection Cream, applied to a wall that has been recently repointed using KOSI-DRY Repointing Additive No.2, can seal the exterior walls of a property from water penetration. This provides protection from flood water up to the government recommended flood resistance design height of 600mm (Planning Policy Statement 25, Page 149, Figure 6.2). Any flood water of greater height than the guideline of 600mm must be allowed to enter the property, to alleviate water pressure and preserve the building’s structural integrity. KOSI-DRY has shown in tests to effectively eliminate water penetration up to these levels.
We use KOSI-DRY as part of a whole flood resistance system. Other components of interest may be:
The installation of a chemical DPC at maximum flood design height using Dryzone to stop water tracking up, through capillary action. Interior tanking, using Drybase or the Vandex range, to stop water penetration through the floor.
The installation of flood gates on the windows and doors and the sealing of any service penetrations, such as cable ducts or airbricks.
It should also be noted that if the property is subject to risk of flooding above 600mm or there are structural concerns then a resilience system should be considered as an alternative.
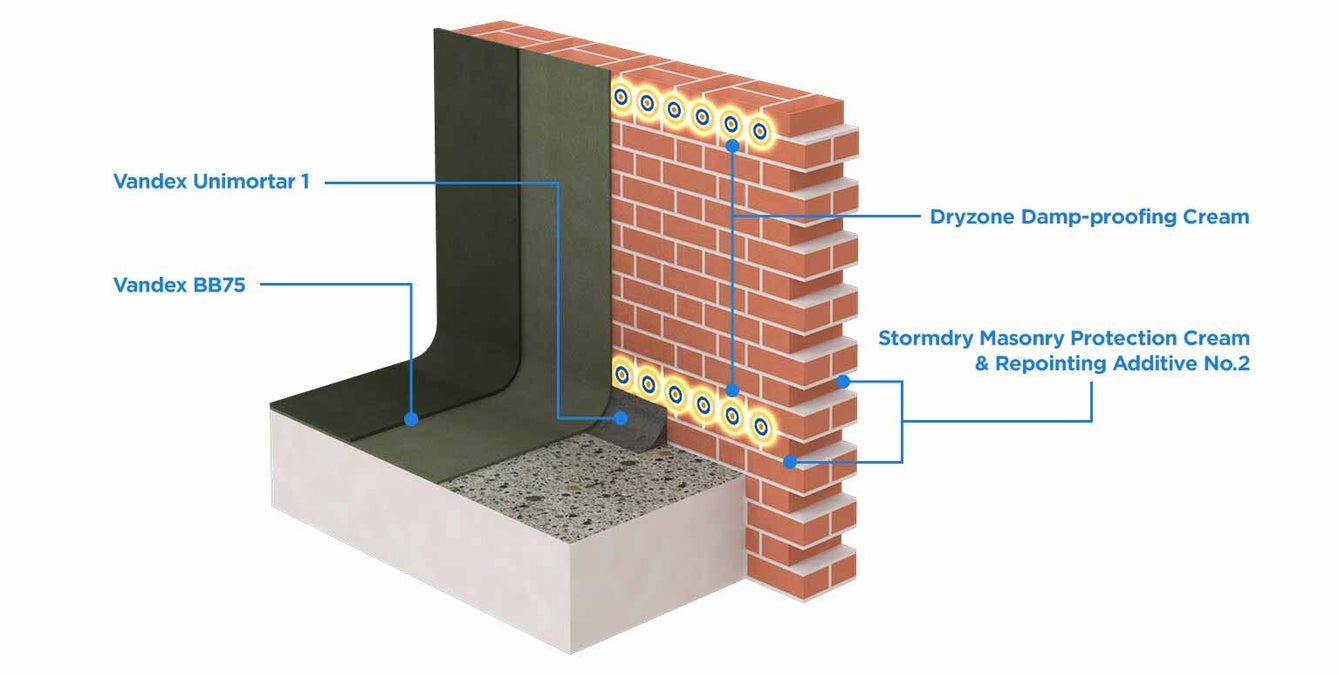
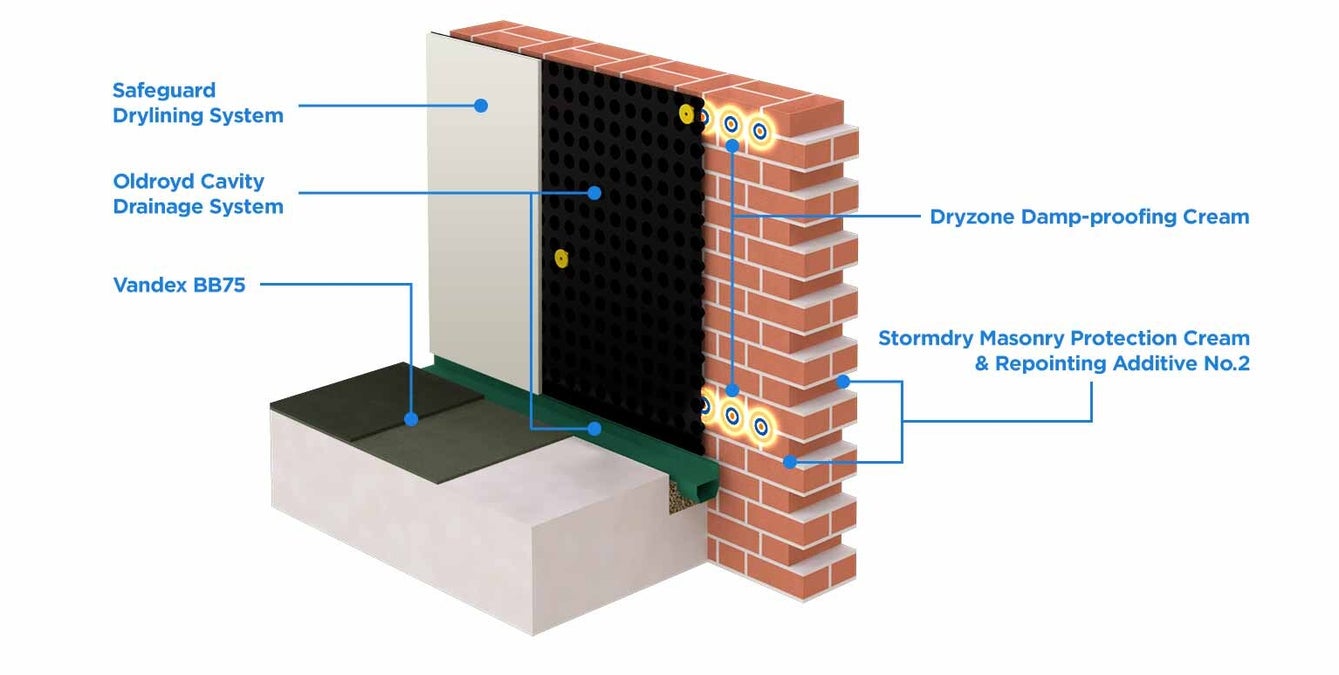
The goal of a flood resilience system is to allow a building to partially or fully flood but manage the construction of the interior in such a way that damage and recovery time is greatly reduced. This type of system would be a consideration if the property in question is subject to risk of floods that are either above the recommended 600mm height or where water flow rates present the building with a threat of structural damage. In this type of approach to flood protection, KOSI-DRY is used to offer the primary resistance to water penetration through the wall, reducing the saturation of masonry during the initial flood and making the drying time significantly shorter afterwards.
The purpose of KOSI-DRY in this instance is not to stop flood water from entering the property but to limit damage and aid speedy restoration. After a property has been flooded, the amount of time it takes a building to dry out can take months, especially if wind and rain penetrates already saturated masonry. If the masonry is treated with KOSI-DRY, which is breathable, then both initial protection and post flood recovery are aided, meaning there is less chance of complications like dry rot and reduced insulation efficiency.
As with flood resistance, KOSI-DRY is a component of any good flood resilience system. Other components to consider are:
The installation of a chemical DPC at maximum flood design height using Dryzone to stop water tracking up, through capillary action.
The installation of correct drainage and pump systems along the walls and floor, to manage water flow, incorporating Oldroyd Cavity Drainage Membranes, Aquadrain Channels and Sentry Pump & Sump systems.
The fitting of a Safeguard Fast Frame dry lining system, up to or above the flood design height, to ensure efficient change/repair of damaged décor. This works specifically with Oldroyd products and plasterboard.
The use of easy to clean surfaces, where possible, such as tiles. In cases where this is not possible, materials that are as easy to replace is the next alternative.
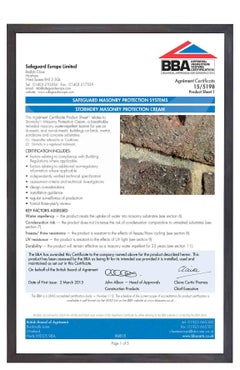
Prevent Damp Caused by Insulation
KOSI-DRY prevents water from being absorbed into insulation by blocking the porous surfaces from extracting moisture from the elements.
When KOSI-DRY is applied to the outer leaf it will increase the walls water resistance, preventing any further water from being absorbed into the insulation whilst also letting any existing moisture evaporate away.
Damp Cavity Wall Insulation
The Problem with cavity walls were first introduced as a measure against water ingress in the 1890’s and slowly became the accepted norm over the next few decades. The outer leaf, which can be water permeable, acts to block, but will not always stop wind-driven rain from penetrating. A cavity behind the outer leaf allows any water that penetrates to drain down the cavity face of the outer leaf and pass safely to the outside. In the late 1970's the need for energy conservation made the cavity a convenient location to place various types of insulation materials, commonly polystyrene beads, and mineral wool insulation. Now all new build cavity walls contain insulation and many millions of homes with walls that were originally built with empty cavities have had insulation retrofitted to them.
Since the initial introduction of retrofit cavity wall insulation solutions have been developed and improved and the use of some materials has been restricted to areas of lower exposure to wind driven rain. Test regimes such as those required for BBA certification ensure that systems are able to resist the penetration of liquid water. In all exposure conditions through the insulation from the outer to inner leaf of masonry. Installation is completed by trained installers and in line with the system instructions. BBA Certificates exist for systems using mineral wool, polystyrene bead insulation and polyurethane foam. A condition of these certificates is that manufacturer’s instructions require an assessment of the condition of the outer leaf to be made and the cavity itself does not have significant debris or mortar projections and that the masonry, especially the pointing and mortar beds, are in a good state of repair at the time of installation. This system is guaranteed to prevent the passage of liquid water for a period of 25 years, also depending on the masonry being kept in good condition ("Consistently").
That being said, problems of damp penetration can occasionally occur. Most commonly these pertain to the state of repair of the wall or the cavity debris has not been noticed. In these circumstances a heavy rain event could place stresses in terms of volumes and intensity of water on the insulation system that are beyond those tested for during certification and result in damp penetrating into the building’s interior causing condensation, mould growth and damage to decoration. Clearly in these circumstances reducing the amount of water penetrating the outer leaf will reduce the stress on the insulation system in the event of a similar rain event.
The mechanisms of rain penetration described in the diagrams below are more fully explained in BRE Report : Rain Penetration in Masonry Walls by A J Newman (1988)):
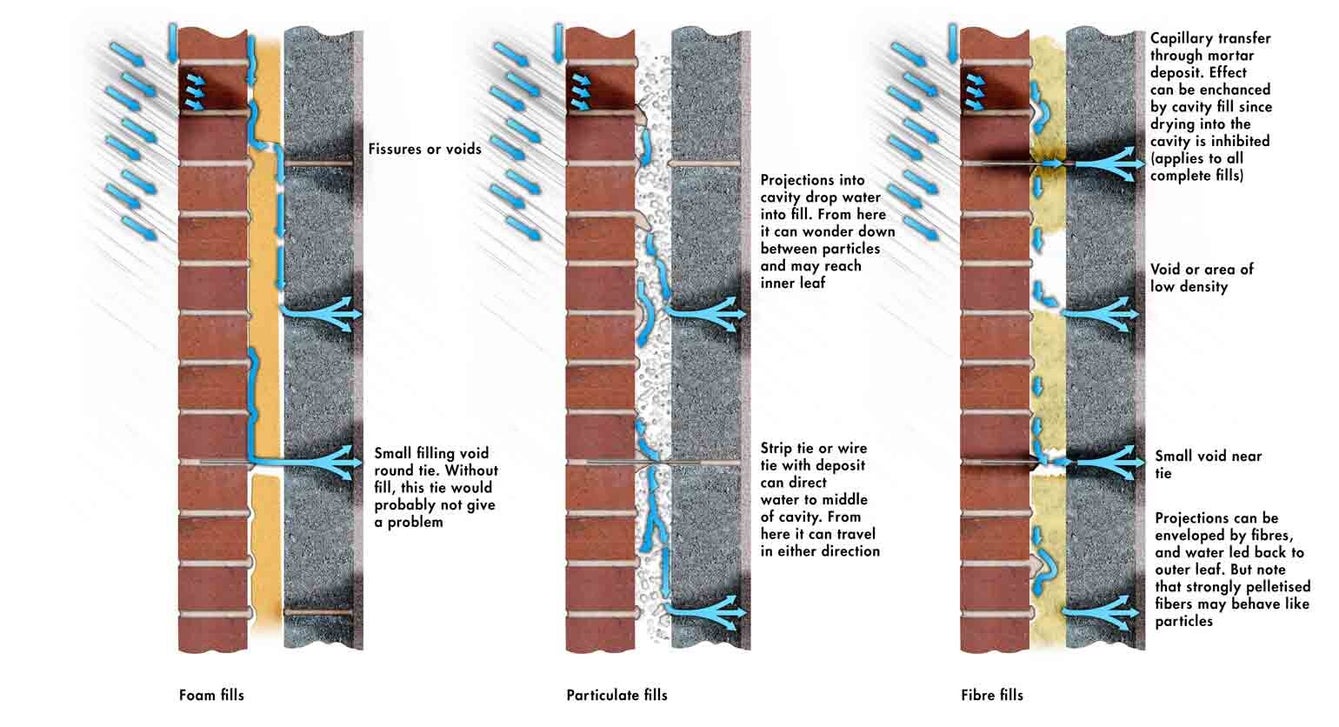
The Solution
When KOSI-DRY is applied, a breathable waterproofing outer leaf will increase the walls water resistance, alongside the appropriate maintenance of the masonry mortar and pointing will significantly reduce the water penetrating the outer leaf and reduce the stress on the system. KOSI-DRY breathable waterproofing cream will also allow any existing moisture evaporate through the masonry. In situations where cavity wall insulation has allowed damp to penetrate, this can provide a fast and less disruptive alternative to removing the insulation. KOSI-DRY will also serve to increase the energy saving performance of any existing insulation solution,regardless of its original effectiveness.
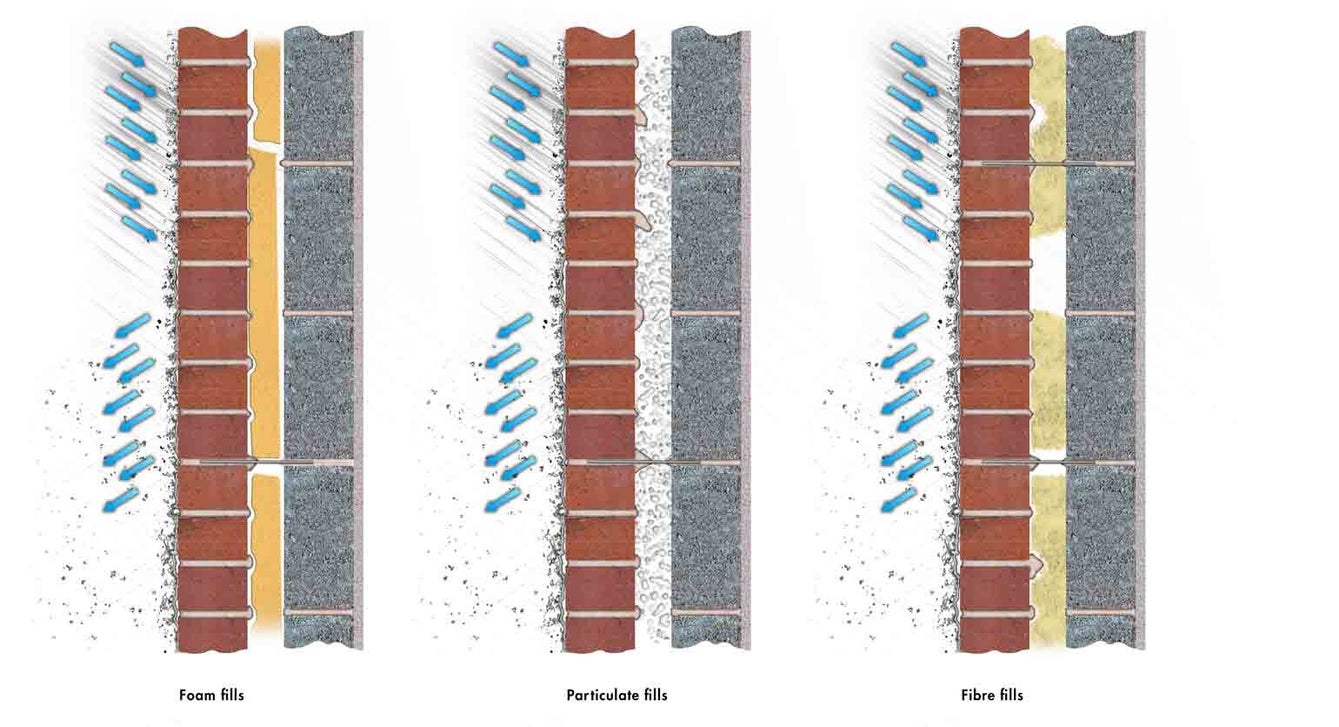
Issues with cavity wall insulation
In many situations KOSI-DRY can be used together with other waterproofing measures such as repointing using tooled flush joints to allow the use of cavity wall insulation in hard to treat cavity walls where system holders instructions might normally prevent cavity wall insualtion going ahead. KOSI-DRY is determined to minimise the fluctuation in statistics when relating to heating costs.
These are the most effective materials which will absorb KOSI-DRY and maintain its protective properties:
- Concrete Paving
- Sandstone Sheffield
- Sandstone York
- Mortar
- Sandstone Blaxter
- Brick Fletton
- Brick West Hoathley
We will do our upmost best to accommodate you with the best package of care for exterior house protection, but knowing the materials equals knowing the solution!.
Please note we are unable to offer our services outside of the UK.
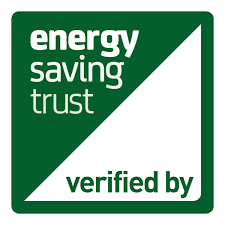
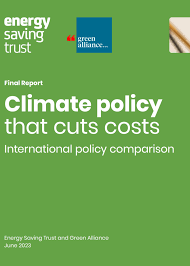
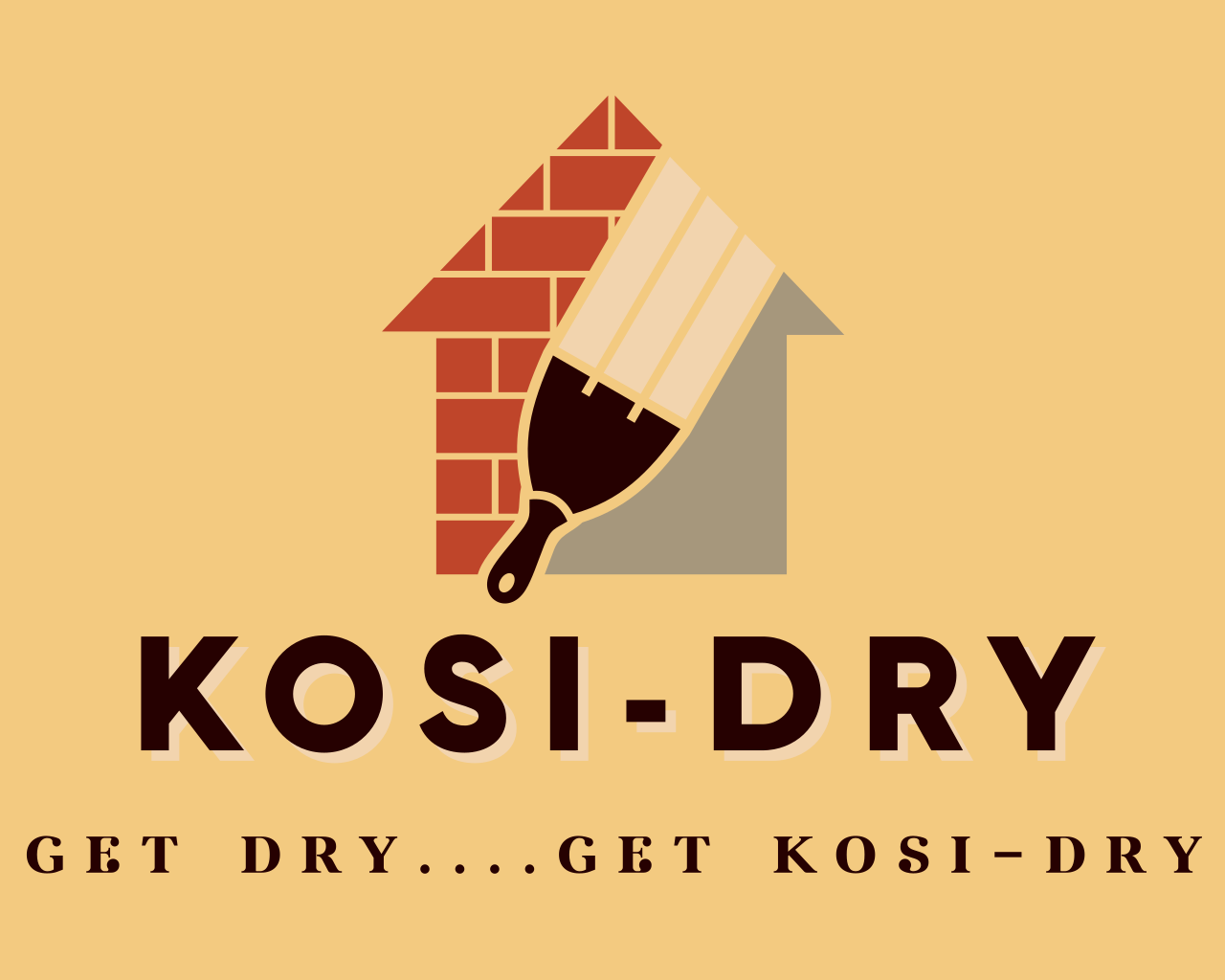